Brewing exceptional beer takes exceptional craftsmanship, requiring a multi-step process of controlling both hot and cold temperatures with absolute precision. The entire brewing process can have temperatures range from 10°C to 76°C (50°F to 170°F). Consequently, insulation plays a vital role in how precise a brewery can control temperatures at each step.
Take the fermentation process of yeast, for example. When yeast consumes sugar, it produces alcohol, carbon dioxide, and heat and can take anywhere between 7 to 21 days. Depending on the environment’s temperature, yeast can impart different flavours into your beer, drastically affecting the final taste. Higher temperatures introduce fruity flavours and can taste quite different than beer fermenting at lower temperatures. This may be desirable or undesirable depending on the type of beer you want to produce. If your beer has a distinct, iconic taste, creating a temperature-controlled environment for yeast to thrive while accounting for excess heat produced during the fermentation process should be of utmost importance. Selecting the right insulation for your fittings can make this process easier and more consistent.
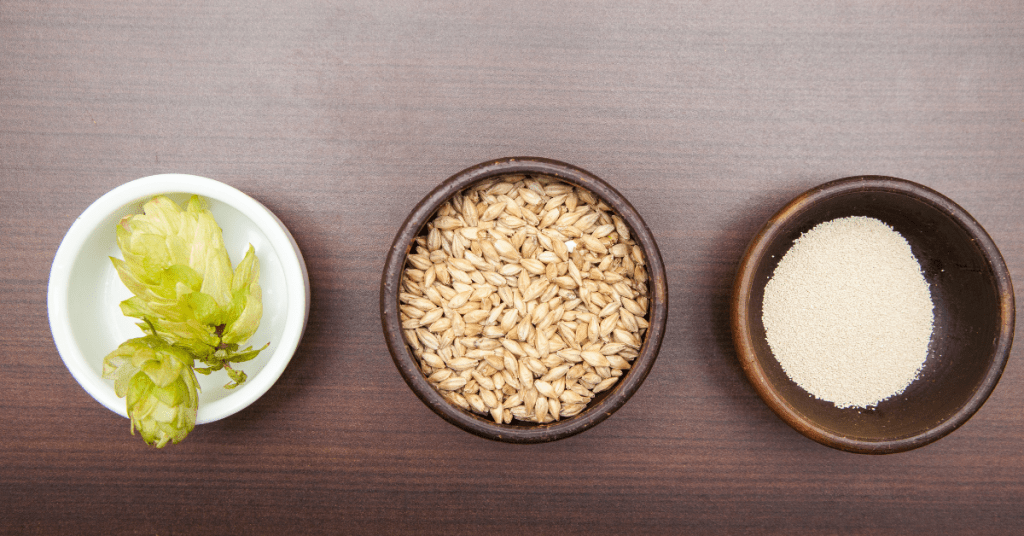
Hops, Malt, and Yeast
Brewing systems require exceptionally clean and controlled environments to ensure the taste is consistent and to reduce the risk of contamination. This subjects instruments to hot, caustic cleaning solutions on a regular basis. Building a custom insulation solution to handle these types of conditions allows you to choose the right materials for your needs. For external materials, polytetrafluoroethylene (PTFE) can be an excellent choice because of its high caustic and temperature resistance. For the insulation within your blanket, consider a material that can handle humid or wet conditions like mineral wool.
Other components carrying coolants or hot fluids must be insulated as well. Leaving them uninsulated creates a safety hazard for personnel where accidental bumps can result in burns or ice burns. In addition, uninsulated temperature control systems will need to work significantly harder to maintain proper temperatures, reducing the instrument’s overall efficiency.
Precise temperature control is the key to brewing an exceptional beer. SUM Ltd’s industrial insulation blankets can assist you in maintaining desirable temperatures. During our design process, SUM Ltd will sit down with you and recommend various materials capable of handling your specified conditions. Our trained specialists will then meet you on-site to precisely measure your instrument and match every bend, curve, or loop it may have. After all, we are firm believers of measuring twice and cutting once. Finally, you can rest assured knowing your new insulation will fit snugly to your instrument. If personnel require access to the instrument for routine maintenance or repairs, SUM Ltd’s custom insulation is easily removed and reapplied within minutes.
Whether your instrument is situated outdoors and needs protection against the elements, or you need insulation to protect equipment as the last line of defence against fire-related incidents, SUM Ltd has a custom industrial insulation solution for you. Book a consultation with us today and learn more about how we can assist your brewery.