Everyone wants a quality product, and all companies claim to produce the best. How do you know which company does? You have standards that your clients, investors and employees expect. Choosing the wrong supplier or manufacturer could be costly to your business in schedule delays, equipment replacement and more. By presenting its ISO 9001 certificate, a company is demonstrating that they are serious about superior standards and have procedures in place to offer a high-quality product.
At SUM Ltd, our motto is “measure twice and cut once.” We are meticulous in our preparation and execution of manufacturing tasks. This is ingrained in us as a company, which is why it is important that we adhere to ISO 9001 standards. What does that really mean for you as the customer?
What is ISO 9001:2015?
ISO 9001:2015 is a Quality Management System (QMS) that offers a quality assurance model for manufacturers and many other industries around the world. It is important to note that ISO does not certify companies. The International Accreditation Forum (IAF) is the governing body that certifies companies have met the ISO 9001 requirements. The standard is reviewed and changed periodically to continue to meet the needs of customers as technology changes. The last time it was revised was 2015 and it is currently being reviewed. Though it does not lay out objectives or values a company must follow, it gives a detailed outline for how a company should organize their business for best practice. It includes a template for leadership, planning, support, operation, performance evaluation, and improvement. All these things contribute to a corporate vision of excellence which translates to great customer service. The customer is at the centre of the ISO 9001 framework.
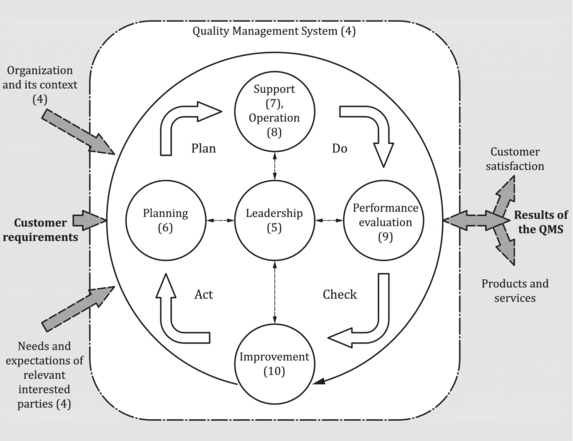
Standardized Processes
Quality products do not just happen. Thorough planning stages and vetting procedures go into each offering. Establishing a standardized process allows a company to refine tasks and correct errors proactively. ISO 9001 lays out a framework that is easy to follow and maintain. This gives companies a map to produce instructions for employees to follow. When employees have a clear understanding of procedure, quality is the same regardless of who is working, and errors are dramatically reduced. The Seven Basic Quality Tools found within the QMS system allow leadership to identify roots of problems by revealing common patterns. This means the customer gets the same quality product every time.
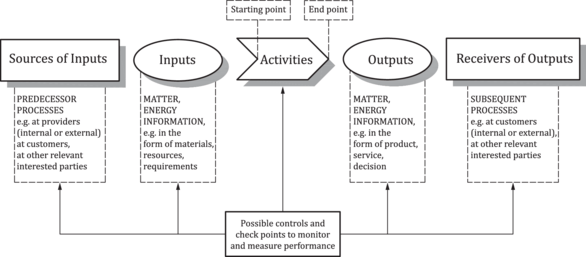
Reliable Products Delivered on Time
Following a specific framework ensures that a strict schedule is followed. How often have you wondered what happened to your order? This type of guesswork is stressful when a project timeline depends on equipment delivery. With a QMS system, there is no guessing about where an order is, if it is completed or if it will have errors when it arrives. An ISO 9001 company knows how long each specification will take, the materials required, and the delivery timeline. The quality management system ensures that products are reliable and error-free upon leaving the facility. You can plan around the delivery date with peace of mind.
Strong Leadership
ISO 9001:2015 requires that leaders not only support the Quality Management System, but also have a direct hand in creating and maintaining it. Leaders must take accountability for the effectiveness of the QMS, empower other leaders and employees to follow the system, ensure it aligns with the company values, foster risk-based thinking, and implement continuous improvement. This means that a manager will have a direct understanding of what an employee must do to fulfill an order and can speak directly to your concerns.
Safety
When an ISO 9001 company standardizes processes and creates reliable, quality products, safety naturally follows. In Alberta, Certificate of Recognition (COR) Certification shows that a company has undergone an Occupational Health and Safety (OHS) audit of their health and safety management processes. Safety is paramount to SUM Ltd and our employees, so we have chosen to be COR Certified in addition to ISO 9001:2015.
Customer Satisfaction & Cost Savings
All these things lead to the most important thing – you, the customer. As an ISO 9001 certified company, the focus is on your needs as a customer. Each element of the framework has been developed in order to meet and exceed your requirements. The goal of a QMS is to bring you a quality product with backing from a knowledgeable and empowered team. Each time an error is made, a miscommunication occurs, or a delivery is late, it costs you money. With an ISO 9001 company, there is a plan to address all these concerns and reduce the frequency of them to next-to-none. Choosing the right manufacturer ends with your needs being met and your budget balanced.
Is SUM the one for you?
SUM Ltd prides itself on its ISO 9001:2015 certification and the commitment to excellence that this brings. Every cut we make is premeditated. Every employee is trained to understand the value of our product offering. We are organized, efficient, and quality focused. Contact us today to discuss your unique needs.