Quick Links:
How were Velcro fasteners invented?
What are the benefits of using Velcro fasteners for custom insulation blanket Materials?
How do I properly care for custom removable insulation blankets with Velcro fasteners?
How are stainless steel wire fasteners created?
What are the benefits of using stainless steel wire fasteners for your custom Insulation blanket materials?
What are the applications for stainless steel wire fasteners?
How do I install stainless steel wire fasteners onto my equipment?
What is stainless steel mesh?
Stainless steel families & grades
What are the benefits of using stainless steel mesh for your custom insulation blanket materials?
What are the applications for stainless steel mesh?
What are silica textiles?
What are the benefits of using silica textiles?
What are the applications for silica textiles?
What are fiberglass textiles?
What are the benefits of using fiberglass textiles?
What are the applications for fiberglass textiles?
What is mineral wool?
What are the benefits of using mineral wool insulation?
What are the applications for mineral wool insulation?
Looking for your own custom insulation blanket Materials? At SUM Ltd. we use a variety of different fasteners and textiles to suit the needs of each custom insulation job. We take into consideration how fast you need access to your instrument, the environment in which your instrument resides, your insulation needs, and the shape and size of your instrument when selecting the materials needed for the job. By Using these criteria, our team will craft the perfect insulation blanket according to your needs.
At SUM Ltd. we aim to provide top quality products for our customers. We work together with our clients to ensure that timelines are met as well as quality service is top tier. Our team guarantees you exceptional services to assist you in getting the job done. We aim to make your job easier and to offer a helping hand
Velcro Fasteners
Some of the benefits to using Velcro fasteners include the cost-effective price, ease of installation, speed of insulation, and the fact that there is no metal required. Looking for your custom insulation blanket materials? Velcro Fasteners are an excellent material solution.
While Velcro fasteners can be used as the primary fastener of your custom removable insulation blanket, it is often used as a complementary fastener. Stainless steel lacing wire with rivets or Teflon straps with D-rings will add extra protection as your company’s need for better thermal protection increases. Of course, we are always here to help guide you through the decision-making process.
Proper care for Velcro fasteners involves limiting exposure to dust that can clog the hook and loop closure mechanism. Additionally, you want to make sure that the nylon/polyester hooks do not come into contact with high temperature surfaces which can melt them.
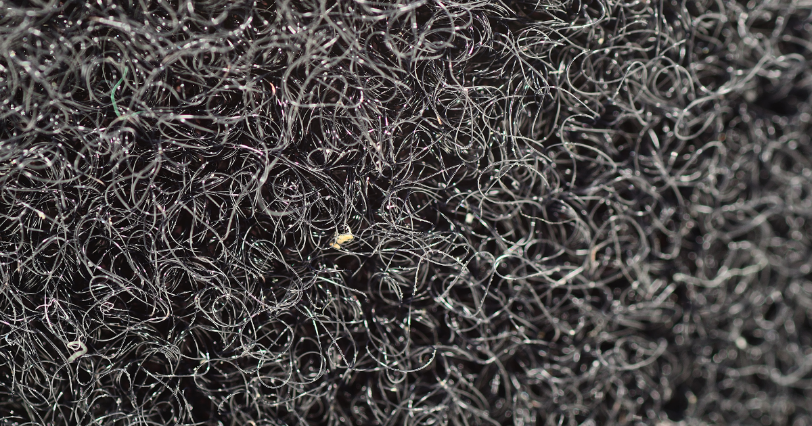
How were Velcro fasteners invented?
Velcro fasteners were invented as the result of a hunting trip in 1948. During this adventure, both, George de Mestral, and his dog became covered in burs from a burdock which were challenging to remove. Curious as to how the biomechanics worked, he examined the specimen under his microscope and found hundreds of tiny hooks that would catch on anything with a loop. More notably, however, was that this mechanism was found to be reversible and repeatable without losing degradation. After 10 years of trial and error and several prototypes, the first viable hook and loop mechanism was born.
Mestral originally created his hook and loop system from cotton; however, after only a few attempts, the system would degrade and eventually fail. Mestral sought after a stronger material to improve its lifespan. Depending on the application, hook and loop systems are generally made from three materials: Nomex, polyester, or nylon.
- Nylon: Durable, hydrophobic, and lightweight material, nylon is capable of withstanding high temperature variations, but is susceptible to ultraviolet light.
- Polyester: Polyester hook and loop systems are hydrophobic, lightweight, and resistant to ultraviolet light; however, the material has a low tolerance to high temperatures.
- Nomex: Developed by the DuPont chemical company, Nomex is a flame-resistant meta-aromatic polyamide (also known as m-aramid) material capable of withstanding up to 350°F or 177°C.
When it comes to manufacturing the material itself, there are two sides to consider: The hook side and the loop side. For the hook side, monofilaments of nylon or polyester are weaved under hot, infrared light, creating a loop. This loop is trimmed so that a hook is created. The area to cut and create the hook must be precise to adhere to the loop side. Inaccurate cuts could lead to faster material degradation and a less effective product. The loop side, or the soft side, is comprised of several thinner monofilament loops, creating a non-uniform appearance.
What are the benefits of using Velcro fasteners for custom insulation blanket Materials?
There are several key advantages to using Velcro fasteners on your next custom removable insulation blanket:
- Price: Velcro fasteners are a cost-effective solution to bind your insulation blanket to your equipment when compared to other fastening system alternatives.
- Tool-less ease of installation: Custom removable insulation blankets with a Velcro fastening system do not require special tools to install.
- Speed of installation: Velcro fasteners require only 5 minutes to remove, allowing personnel to perform monitoring, maintenance, or routine inspections quick.
- No metal required: This is particularly useful if the insulation is covering certain kinds of steel or is touching sensitive equipment.
While Velcro fasteners can be used as the primary fastener of your custom removable insulation blanket, it is often used as a complementary fastener. Stainless steel lacing wire with rivets or Teflon straps with D-rings will add extra protection as your company’s need for better thermal protection increases. Of course, SUM Ltd is always here to help guide you through the decision-making process.
How do I properly care for custom removable insulation blankets with Velcro fasteners?
As Velcro fasteners are made of nylon or polyester hooks, care should be taken to ensure the nylon/polyester hooks do not come into contact with the hot surface of your equipment. Custom removable insulation blankets with Velcro fasteners should always be installed onto your equipment when it is cold to the touch. In addition, ensure the exposure of grime, dust, or other contaminants is mitigated in the Velcro fastening system. Failing to do so may render it ineffective or result in total failure.
Stainless Steel Wire Fasteners
Stainless steel wire fasteners are one of our most popular fastening systems. They secure removable insulation blankets around an instrument and are notable for their durability, resistance to corrosion and excellent tensile strength. Stainless Steel is an excellent choice when choosing your custom insulation blanket materials.
The benefits of using this resilient material in your custom insulation project include cost-effectiveness, plasticity, and high resistance to corrosion. With this style of fastener, proper installation is key. If you are interested in integrating stainless steel wire fasteners into your next custom removable insulation blanket, we can help and walk you through the process step by step.
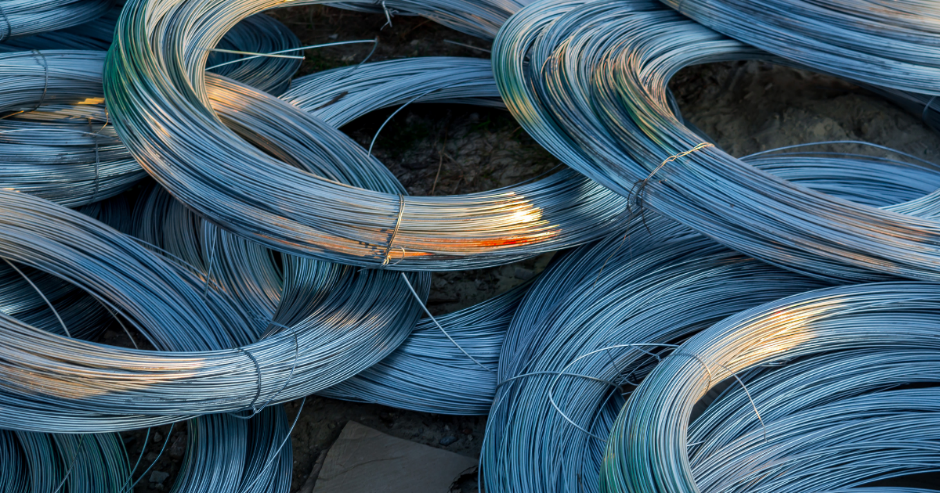
How are stainless steel wire fasteners created?
To begin, stainless steel is treated in a consistent, high-temperature environment for a set duration of time called soft annealing. The duration in which the material stays in this environment depends on the thickness of the wire. Soft annealing heats the metal above its recrystallization temperature, but below its melting point, causing new grains to form without any residual stresses. Once the inner core has reached the appropriate temperature, the metal is slowly cooled for new grains to develop. The result is steel that is more workable, reduced hardness, and increased ductility (a material’s ability to draw into a wire.)
Stainless steel wire fasteners provide several benefits which include:
- Cost: Stainless steel wire fasteners are a cost-effective, semi-permanent solution to insulating instruments.
- Plasticity: Stainless steel wire fasteners are highly plastic, capable of bending or tying the wire into any configuration, as necessary.
- High corrosion resistance: Thanks to its natural properties, stainless steel wire fasteners are highly resistant to corrosion.
What are the applications for stainless steel wire fasteners?
- Corrosive environments: Stainless steel forms a passive oxide layer, rendering the surface electrochemically passive in the presence of corrosive environments.
- Heat conservation: Stainless steel wire is capable of handling elevated temperatures without warping or losing structural integrity.
- Employee Personal Protection: Wire fastening systems reliably secure insulation blankets around high-temperature instruments, mitigating the risk of burns.
How do I install stainless steel wire fasteners onto my equipment?
Proper installation is important to ensure your blanket functions properly and operates optimally. Exposed areas of your instrument may result in a less efficient product.
Follow these steps for optimal installation of your removable insulation:
- Before installation, ensure you have a wire twisting tool to create loops in the following steps.
- Form and compress the blanket around the instrument. Continue working your way around the instrument until the seams of each end of the blanket are as close as possible to one another.
- Form a loop with the stainless-steel wire fastener and hook it around the first rivet.
- Pull and wrap the steel wire around the second rivet, ensuring it is tightened and secured. Continue lacing the wire around each rivet, alternating between each end until you reach the length of the blanket.
- Cut and wrap any excess wire around the final rivet.
Stainless Steel Mesh
Stainless steel mesh is a type of casing used in custom removable insulation blankets designed to protect instruments from a variety of elements. The mesh can be made up of several types of alloys with varying concentrations of each to create an extremely versatile, durable, and affordable insulation material. When choosing your custom insulation blanket materials, stainless steel mesh is another great choice.
The key benefits of this material include temperature resistance, corrosion resistance, and formability. If these are the properties you require for a casing in your next custom insulation blanket, we build long-lasting and efficient custom-fitted insulation blankets for your needs.
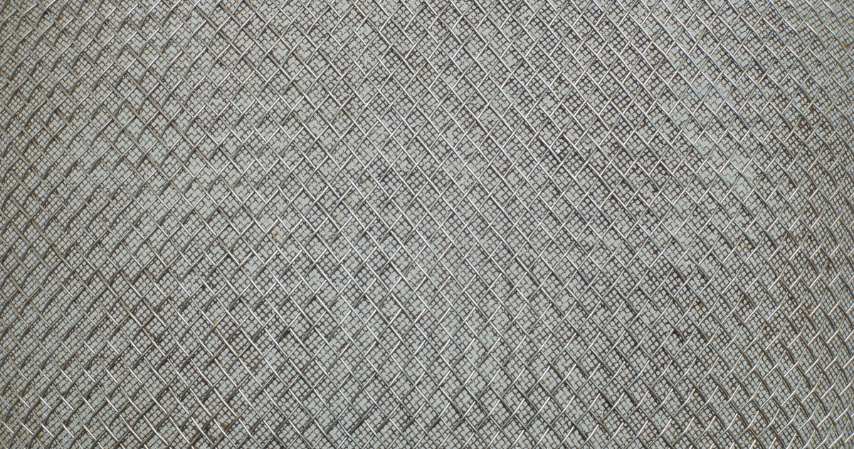
What is Stainless Steel Mesh?
Stainless steel mesh is a type of casing used in custom removable insulation blankets designed to protect instruments from a variety of elements. Stainless steel mesh is most commonly manufactured using 304 grade austenitic stainless steel, but depending on the insulation blanket’s requirements, other grades may be used.
Stainless steel family & grades
Before we begin to understand stainless steel mesh, we first need to understand the properties of stainless steel itself. Depending on the client’s specific needs, varying compositions of alloying metals may offer a differing set of properties than another. These varying compositions are categorized by grades. For example, within austenitic stainless steels, the client may request grade 302 for its greater mix of carbon in their stainless steel, resulting in increased strength, whereas another client may need less carbon in their mix to assist in welding operations. Grades of stainless steel that exhibit desirable traits for its intended application must be considered when producing stainless steel mesh.
Grades are then grouped with stainless steels with similar compositions of alloying elements and properties, known as families. There are four families: Austenitic, ferritic, duplex, and martensitic.
Family #1: Austenitic stainless steel
The most popular of stainless-steel families, austenitic stainless steel consists of 16-26% chromium, 6-12% nickel and iron. Molybdenum, manganese or other alloying elements may also be added to create desired properties. Austenitic grades fall within the 300’s category.
One of the most popular grades of austenitic stainless steel is grade 304. By the standards set by the Society of Automotive Engineers (SAE), it must contain:
- 18% to 20% Chromium
- 8% to 10.5% Nickel
- 0.08% Carbon
- 2% Manganese
- 0.75% Silicon
- 0.045% Phosphorus
- 0.03% Sulfur
- 0.1% Nitrogen
Family #2: Ferritic stainless steel
On a molecular level, ferritic stainless steel receives its name from the soft metal that forms its microstructure, known as α-iron (alpha-iron) or ferrite. Ferritic stainless steel contains a low nickel content, making it more cost-effective than other families, and can contain high concentrations of iron, causing the material to be generally magnetic, depending on its grade. Certain grades can also contain chromium levels as high as 27%. Other metals include molybdenum, niobium, silicon, and/or titanium. You can find ferritic stainless steel used in applications such as petrochemical, heat exchangers, furnaces, and appliances.
Family #3: Duplex stainless steel
Duplex stainless steel combines the desirable characteristics of both ferritic and austenitic families, often at a lower cost. Common components of duplex stainless steel include carbon, manganese, silicon, chromium, nickel, phosphorus, and sulphur. Depending on the grade, molybdenum, nitrogen, and copper may also be found in the final product.
Much like the families it is derived from, duplex stainless steel offers comparable corrosion resistance to that of austenitic grades and higher toughness and ductility than ferritic grades with a lower nickel content. Common applications include, but are not limited to, chemical and liquid processing, naval parts and components, construction, and pulp and paper production.
Family #4: Martensitic and precipitation hardening stainless steel
While martensitic and precipitation hardening stainless steel is the least common of the 4 families, it still demonstrates clear applications such as knives, razors, or medical/dental tools. Martensitic stainless steel can be hardened and tempered through heat treatment due to the added carbon. Other alloying elements include manganese, molybdenum and nickel.
Stainless steel family and grade SUM Ltd uses
While austenitic stainless steel’s superior corrosion resistance is a desirable trait, stainless steel mesh commonly uses this family primarily for its formability. Exploiting austenitic stainless steel’s formability property allows SUM Ltd to build custom insulation blankets to fit snugly to an instrument. As we’ve mentioned in our previous blog, the effectiveness of a removable insulation blanket hinges on the blanket properly fitting the instrument. Loose or improperly fitted blankets may significantly reduce its overall performance or potentially render it completely ineffective.
What are the benefits of using stainless steel mesh?
- Temperature resistance: Stainless steel mesh is capable of handling extremely high temperatures ranges of up to 1,260°C (2,300°F).
- Corrosion resistance: Thanks to its natural properties, stainless steel mesh is highly resistant to corrosion. Certain grades of stainless steel have a lower predisposition to stress corrosion cracking.
- Formability: Drawing stainless steel into thin wires, then weaving it into a mesh, as opposed to using sheet metal, is what offers stainless steel mesh its high formability without the added weight or compromising its temperature resistance. Mitigate gaps between your instrument and removable blanket to improve its overall efficiency with stainless steel mesh.
What are the applications for stainless steel mesh?
- Marine: Due to austenitic stainless steel’s natural ability to resist corrosion, stainless steel mesh is highly Temperature resistance: Stainless steel mesh is capable of handling extremely high temperatures ranges of up to 1,260°C (2,300°F).
- Corrosion resistance: Thanks to its natural properties, stainless steel mesh is highly resistant to corrosion. Certain grades of stainless steel have a lower predisposition to stress corrosion cracking.
- Formability: Drawing stainless steel into thin wires, then weaving it into a mesh, as opposed to using sheet metal, is what offers stainless steel mesh its high formability without the added weight or compromising its temperature resistance. Mitigate gaps between your instrument and removable blanket to improve its overall efficiency with stainless steel mesh.
- suited for marine environments.
- Aerospace: High formability to unconventional shapes, lightweight relative to sheet metal, and rapid removal and replacement for in-service inspection of protected equipment make custom removable insulation blankets with stainless steel mesh casings ideal for aerospace application.
- Heat conservation: Minimize process disturbances and energy loss using a custom removable insulation blanket with a stainless-steel mesh casing.
- Employee personal protection: Adding a barrier such as our custom removable insulation blankets between equipment with high temperature surfaces drastically reduces the risk of burns.
Silica Textiles
Lightweight, refractory, and durable, silica textiles are long-lasting textiles used to protect instruments operating at extreme temperature ranges for a variety of industries, resulting in reduced energy expenditures. Silica textiles come in two different weaves: plain weave, and twill weave. Plain weave creates a rigid textile that does not easily unravel, while twill weave forms a more pliable and flexible weave. For your custom insulation blanket materials, silica textiles are a great choice.
Some of the key benefits of using silica textiles is its durability, water and oil resistance, chemical resistance, high temperature rating, and ease of use. With applications in heat conservation and employee personal protection, this material is extremely helpful to incorporate into your workplace processes for safety and cost savings.
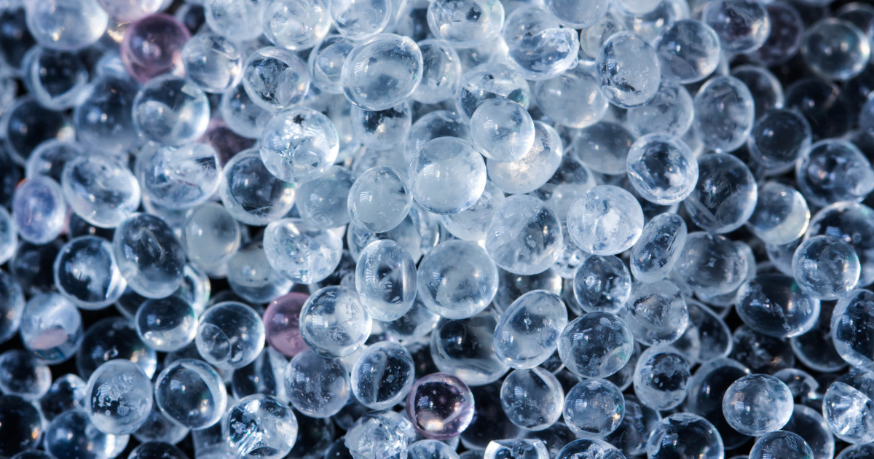
What are silica textiles?
Containing 96% of amorphous silica and traces of other elements, Silica textiles use a continuous filament of silica woven to keep its strength and flexibility within high temperatures environments of up to 1,000°C (1,800°F) of continuous exposure and only begins to melt at temperature of 3000°F (1649°C).
There are three types of crystalline orientations: Crystalline, polycrystalline, and amorphous. Crystalline is an atomic structure that repeats periodically across its whole volume, regardless of its length. Common examples of crystalline solids include sodium chloride, diamonds, and sodium nitrate. A polycrystalline solid is formed of many crystallites (also known as grains) across a length scale. When each crystallite is thought of as an individual crystal, a polycrystalline solid can be seen as several crystallites. Most inorganic solids are polycrystalline, including all common metals, alloys, and many ceramics. Amorphous solids lack a clearly defined shape or form of atoms with an infinite translational symmetry in all three dimensions. Applied external forces cause the solid to bend, twist to distort its shape, but reverts to its original shape after the force is removed. Examples include glass, gels, rubber, and plastic. While silica can be found in both crystalline and amorphous forms, silica textiles benefit greatly from both the high tensile strength and flexibility of amorphous silica.
Silica textiles are woven using a 4-harness satin (also known as crow’s foot) weave. Satin weaves are the most pliable weave due to less frequent over/under crossings, allowing the textile to form around compound curves more easily. A single filament floats over 3 to 7 times before crossing an intersecting filament. Cutting a satin weave may cause the textile to unravel as each filament is not held as tightly.
There are two other types of weaves:
- Plain weave: Plain weave is one of the most common weaves where each filament crosses over and under alternately as it reaches another intersecting filament. The over/under crossing creates a rigid textile that does not unravel easily when cut or handled.
- Twill weave: Twill weave floats 2 or 3 intersecting filaments before crossing over/under, creating a herringbone design. With less frequent over/under crossings of each filament, twill weave also forms a more pliable, flexible weave than plain weave styles.
What are the benefits of using silica textiles?
Silica textiles offer a variety of advantages:
- Durable: The material properties of amorphous silica provide silica textiles high tensile strength and durability. Coatings are also available to further improve abrasion resistance and tensile strength.
- Water and oil resistance: Thanks to certain coatings, silica textiles are capable of resisting water and oil.
- Chemical resistance: Silica textiles are highly resistant against oxidation and most industrial chemicals except for strong alkalis, hydrofluoric acid and sodium.
- High temperature rating: up to 1,000°C (1,800°F) of continuous exposure and a melting temperature of 3000°F (1649°C).
- Ease of use: The flexibility of amorphous silica filaments allows a silica textile insulation blanket to bend to an instrument’s form with ease.
What are the applications of using silica textiles?
- Heat conservation: For high heat instruments, silica facing insulation blankets minimize process disturbances, energy loss and equipment replacement costs.
- Employee Personal Protection: Adding an appropriately composed silica facing insulation blanket between personnel and equipment can increase productivity in high-heat equipment areas, allowing employees to continue working at longer intervals.
Fiberglass Textiles
Throughout history, glassmakers have experimented with creating strands of glass fibers, pushing how fine a single strand of glass could be. The first fiberglass insulation product meant for commercial use was invented by Games Slayter nearly a century ago. At today’s scale of production, fiberglass and fiberglass textiles are only made possible through fine machine tooling. When choosing your custom insulation blanket materials, fiberglass is another great choice.
Fiberglass textiles is one of SUM Ltd.’s most popular materials for building industrial and commercial insulation. However, fiberglass can also be used as material reinforcement, electrical insulation, and even data transmission, leading to its reputation as a versatile material. In our previous blog, we discussed fiberglass as an insulation product. By weaving fine strands together, fiberglass can also be transformed into a textile.
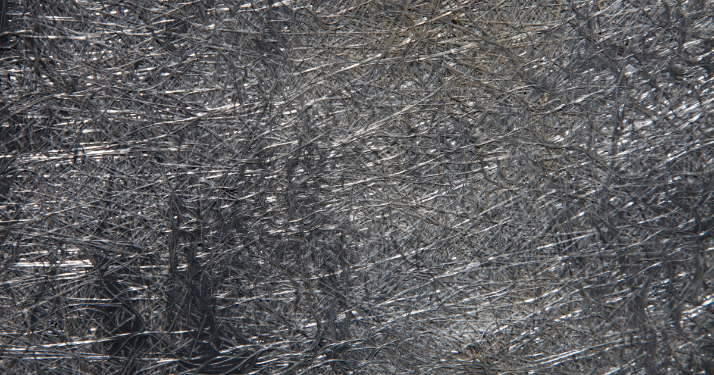
What are fiberglass textiles?
Fiberglass textiles are fabric-like materials made from weaving exceptionally fine glass fiber threads only a few microns thick. Thanks to their high tensile strength and pliability, fiberglass textiles can be used to strengthen products—even products with bends, curves or unusual shapes.
Fiberglass textiles are also highly effective thermal insulators and—when paired with an insulation material in a custom removable insulation blanket—can withstand high temperatures to protect employees or equipment.
Fiberglass textiles come in various weaves, depending on the customer’s needs:
- Plain weave: Plain weave is one of the most common weaves where each glass fiber crosses over and under alternately as it reaches another intersecting fiber. The over/ under crossing of the threads creates a rigid textile that does not unravel easily when cut or handled.
- Twill weave: Twill weave floats 2 or 3 intersecting fibers before crossing over/ under, creating a herringbone design. With less frequent over/under crossings of each thread, twill weave also forms a highly pliable weave that is stronger than plain weave styles.
- Satin weave: Satin weaves are the most pliable weave due to even less frequent over/under crossings. A single thread can float over 3 to 7 threads before crossing an intersecting fiber. Cutting a satin weave may cause the textile to unravel as each thread is not held as tightly.
Fiberglass textiles also come in a variety of different compositions that offer different properties:
- S-glass: Developed with a higher percentage of silicon dioxide than other variants, s-glass is designed to offer strong mechanical properties and withstand high temperatures.
- C-glass: Containing calcium borosilicate, C-glass was developed to have a high chemical resistance and handle corrosive environments.
At SUM Ltd, we specialize our fiberglass textiles offering for thermal insulation purposes.
What are the benefits of using fiberglass textiles?
- Lightweight: The diameter of individual fiberglass strands are only a few microns, making it extremely lightweight.
- High tensile strength: Using a variant with improved mechanical properties, such as S-glass, offers between 2 to 4.5 gigapascals of tensile strength.
- Thermal insulation: Fiberglass textiles can handle up to 1800°F (980°C) of continuous heat.
- Easy installation process: When deciding to use fiberglass textiles as part of your custom removable insulation blankets, our tool-less design requires only 5 minutes to remove, allowing staff to perform monitoring, maintenance, or routine inspections easily.
What are the applications for fiberglass textiles?
- Heat conservation: Minimize process disturbances and energy loss using fiberglass textiles.
- Employee personal protection: Adding a fiberglass textile insulation blanket between personnel and equipment can drastically reduce the risk of burns.
- Freeze protection: Fiberglass textiles as a component to a custom heat-traced blanket provides excellent resistance to extreme weather conditions.
Mineral Wool
Material choice can play a vital role in the longevity and performance of a custom removable insulation blanket and SUM Ltd offers a wide range of materials to choose from. From attenuating sounds to insulating against high temperatures, mineral wool insulation is one of our most popular insulation materials to use. Mineral wool is our most popular choice when it comes to deciding on your custom insulation blanket materials.
It was by chance that mineral wool was discovered. More than half a century ago, it was observed that volcanic lava from an erupting volcano could be whipped into wooly tufts by prevailing winds. Shortly after, factories replicated this process to produce the insulation material we know today.
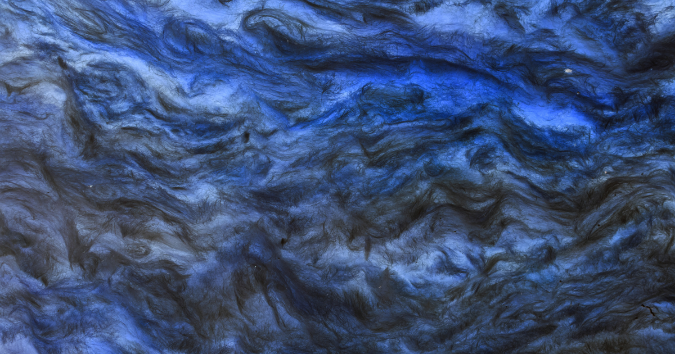
What is mineral wool?
Mineral wool is non-metallic, inorganic, water-repellent insulation material consisting of basalt rock, slag, and a resin binder. Coke, a grey, hard and porous material with a high carbon content, is used as fuel to heat these ingredients as hot as 3000°F or 1650°C, creating molten lava. This molten lava is whipped into thin strands approximately 15-20 micrometres thick and rapidly air-cooled using an air jet or a spinning wheel. The strands are then combined with a resin binder and reactive hydrophobe to further improve the mineral wool’s hydrophobic properties. Finally, the mineral wool is layered, compressed, and cured to its desired density and thickness, ready to be packaged and shipped.
Mineral wool insulation has several key properties:
- Density: Mineral wool is relatively denser than other forms of insulating material such as aerogel or fiberglass insulation.
- Thermal conductivity: Mineral wool has a low thermal conductivity due to its manufacturing process.
- Water affinity: Mineral wool is naturally hydrophobic as it is made from basalt rock. These hydrophobic properties are further enhanced by combining a hydrophobic compound to the insulation.
- Recycled material percentage: Mineral wool uses approximately 70% recycled materials like slag from the steel industry.
What are the benefits of using mineral wool insulation?
- Sound attenuation: Mineral wool is an excellent material to attenuate mid to high frequencies from internal or external sources.
- Thermal insulation: Insulation blankets using mineral wool can withstand up to 1000°C or 1832°F.
- Water-repellent: As minerals are made from basalt rocks, mineral wool is naturally water-repellent and further enhanced with a reactive hydrophobe.
- Easy installation process: Custom removable insulation blankets with mineral wool insulation is quick and easy to install thanks to its tool-less design. Maintenance and repair personnel only require 5 minutes to remove and reapply blankets.
- High R-value per dollar: Mineral wool insulation has an R-value of 4.6 per inch at a relatively low cost.
What are the applications for mineral wool insulation?
Mineral wool insulation’s versatility offers a wide range of applications:
- Sound Insulation: Using mineral wool as your preferred choice of insulation material can absorb and dampen sounds, significantly reducing noise levels.
- Employee personal protection: Adding a barrier such as mineral wool insulation between equipment with high temperature surfaces drastically reduces the risk of burns. Equipment such as steam pipes and steam traps may also be a high-risk area for employees.
- Fire protection: In the event of a fire, mineral wool insulation can reduce the risk of property and equipment damage for a full 30 minutes.
- High-humidity settings: A mineral wool insulation blanket is capable of handling high humidity due to its hydrophobic characteristics, making it suitable to protect components against water and corrosion.
Conclusion
Conclusion
Each custom insulation project is unique, which is why we carefully consider which materials are needed for every job. We aim to provide our customers with the best possible services by creating our insulation blankets to accurately match your instrument. To us, perfection is the only standard, and a job well done is a blanket that precisely matches every bend, curve, or loop of your instrument. To achieve this, our dedicated staff members always measure and remeasure your instrument. After all, we are firm believers of measuring twice and cutting once.
Our attention to build quality has earned us the trust of companies around the world. You can find our insulation on North Sea drilling platforms, Argentinian instruments, or right at home in BC ships and mines. book a consultation with SUM Ltd today. to get started on solutions for your custom insulation needs.